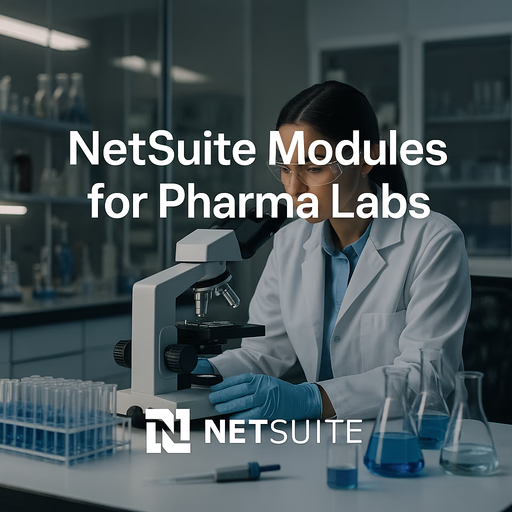
NetSuite ERP Modules for Pharmaceutical Manufacturing Labs (U.S. Perspective)
Introduction
Pharmaceutical manufacturing labs in the U.S. operate under strict regulatory oversight (FDA, DEA, EPA, etc.), requiring robust systems to manage operations and ensure compliance. An Enterprise Resource Planning (ERP) solution can unify lab operations – from production and inventory to quality control and finance – providing the traceability and controls demanded by Good Manufacturing Practice (GMP) guidelines. Oracle NetSuite, a cloud-based ERP platform, has become a popular choice among life sciences and pharma companies because it offers broad functionality and compliance-friendly features in a unified system intuitionlabs.ai. This report provides an educational overview of all NetSuite ERP modules and tools relevant to running a pharmaceutical manufacturing lab, including core modules (financials, inventory, orders, production), industry-specific add-ons (quality management, compliance management, batch records), advanced manufacturing capabilities for GMP environments, support for FDA regulations ( 21 CFR Part 11, GxP), recommended integrations (LIMS, MES, validation tools), scalability considerations, customization/automation, and real-world case examples. All information is tailored to U.S. pharma terminology and regulatory context.
Core NetSuite ERP Modules for Pharma Operations
NetSuite provides an integrated suite of modules covering end-to-end business processes – financial management, supply chain, manufacturing, inventory, orders, and even CRM – all in one platform intuitionlabs.ai. This unified architecture means a pharmaceutical lab can manage everything from procurement of raw materials to batch production and customer distribution in a single system, ensuring data consistency and real-time visibility. Below we outline the core NetSuite modules most relevant to a pharma manufacturing lab:
Financial Management
NetSuite’s financial module handles general ledger, accounts payable/receivable, revenue management, and financial reporting. Pharma labs rely on it for strong financial controls (especially if publicly traded under SOX), budgeting R&D vs. manufacturing costs, and managing grants or contracts. Multi-currency and multi-entity support (NetSuite OneWorld) allows consolidated financials across divisions or global subsidiaries linkedin.com. By having finance tightly integrated with inventory and manufacturing, labs can trace the cost of goods for each batch and maintain audit trails of transactions. NetSuite has been verified to meet key financial control standards (SOC 1/SOX compliance) and can be configured for 21 CFR Part 11 compliant financial approvals as needed intuitionlabs.ai. In practice, this means CFOs and auditors can trust the system’s numbers and controls. For example, Selecta Biosciences used NetSuite to unify its accounting and project budgeting, which improved visibility into cash burn and ensured more resources went toward science instead of manual reporting intuitionlabs.ai intuitionlabs.ai.
Inventory & Lot Management
Inventory management is critical in pharma manufacturing to maintain traceability from raw ingredients to finished drug batches. NetSuite’s inventory module supports lot and serial number management with expiry date tracking, which is essential for compliance with FDA ** cGMP** regulations and the Drug Supply Chain Security Act (DSCSA) for traceability linkedin.com. Each lot of raw material and each batch of product can be tracked through receiving, production, and distribution, creating a genealogy that enables rapid recalls or investigations if needed. The system supports multiple stock locations (e.g. separate quarantined storage for quality holds) and can enforce FEFO (first-expiry-first-out) allocation to reduce expired inventory. Validating the inventory module is crucial for FDA-regulated labs – it confirms that inventory records are accurate and that the system supports full traceability from raw materials to finished goods sikich.com. Key inventory capabilities include real-time stock levels, warehouse management (bins, picking/putaway), and integration of inventory status with quality control (for example, materials can be put on quality hold until QC tests pass). NetSuite’s lot traceability features help maintain compliance by ensuring that for any given drug batch, you can quickly find all related transactions (where used, which orders shipped) – a cornerstone of product safety and recall readiness linkedin.com.
Order Management & Supply Chain
NetSuite’s order management module covers the order-to-cash and procure-to-pay cycles, tying together customer orders, procurement of materials, and fulfillment. For a pharma lab, this means sales orders for products (or internal demand for clinical trial materials) are seamlessly linked to inventory availability and production plans, while purchase orders for raw chemicals, APIs, or lab supplies are managed in the same system. The module ensures efficient and controlled purchasing processes – including vendor management, purchase order processing, receiving inspections, and distribution logistics sikich.com. Supplier qualification can be tracked (via vendor records and custom fields/workflows) to ensure materials are sourced from approved vendors, a GMP requirement. NetSuite can automatically reserve inventory for orders, generate pick/pack/ship tasks, and handle shipping documentation which is important if distributing controlled substances or temperature-sensitive products. On the procurement side, it maintains a complete audit trail of each lot received (linking to COA documents from vendors) and can enforce two-way or three-way match for quality and financial control. Validating supply chain functions is important to confirm compliance – it reduces risk of supply chain disruptions and ensures all steps (from supplier to customer) meet FDA quality and record-keeping requirements sikich.com sikich.com. NetSuite also supports integration with 3PL warehouses and freight carriers, which many pharma companies use for distribution. Notably, there is a Wholesaler Distribution module (suite bundle) that helps pharma distributors comply with DSCSA by automating verification of returned products via a Verification Router Service before resale linkedin.com. In short, the order/procurement modules ensure materials and products flow smoothly while maintaining compliance checks at each step (e.g. blocking shipment of any lot that’s on quality hold or missing DSCSA verification).
Manufacturing (Production Management)
NetSuite’s manufacturing module enables labs to plan and execute production of batches or assemblies. Users can define Bills of Materials (BOMs) or formulas for drug products, create work orders for batch runs, and track production status and yields. The system supports production planning and scheduling to balance resource supply and demand, and it allows defining routing steps with standard times, so labs can schedule work centers and labor. In a pharma context, each work order represents a batch record – capturing components issued (with lot numbers), processing steps, and outputs. NetSuite’s base manufacturing functionality ensures that production processes are controlled and documented in compliance with GMP standardsd through receiving, production, and distribution, creating a genealogy that enables rapid recalls or investigations if needed. The system supports multiple stock locations (e.g. separate quarantined storage for quality holds) and can enforce FEFO (first-expiry-first-out) allocation to reduce expired inventory. Validating the inventory module is crucial for FDA-regulated labs – it confirms that inventory records are accurate and that the system supports full traceability from raw materials to finished goods sikich.com. Key inventory capabilities include real-time stock levels, warehouse management (bins, picking/putaway), and integration of inventory status with quality control (for example, materials can be put on quality hold until QC tests pass). NetSuite’s lot traceability features help maintain compliance by ensuring that for any given drug batch, you can quickly find all related transactions (where used, which orders shipped) – a cornerstone of product safety and recall readiness linkedin.com.
Order Management & Supply Chain
NetSuite’s order management module covers the order-to-cash and procure-to-pay cycles, tying together customer orders, procurement of materials, and fulfillment. For a pharma lab, this means sales orders for products (or internal demand for clinical trial materials) are seamlessly linked to inventory availability and production plans, while purchase orders for raw chemicals, APIs, or lab supplies are managed in the same system. The module ensures efficient and controlled purchasing processes – including vendor management, purchase order processing, receiving inspections, and distribution logistics sikich.com. Supplier qualification can be tracked (via vendor records and custom fields/workflows) to ensure materials are sourced from approved vendors, a GMP requirement. NetSuite can automatically reserve inventory for orders, generate pick/pack/ship tasks, and handle shipping documentation which is important if distributing controlled substances or temperature-sensitive products. On the procurement side, it maintains a complete audit trail of each lot received (linking to COA documents from vendors) and can enforce two-way or three-way match for quality and financial control. Validating supply chain functions is important to confirm compliance – it reduces risk of supply chain disruptions and ensures all steps (from supplier to customer) meet FDA quality and record-keeping requirements sikich.com sikich.com. NetSuite also supports integration with 3PL warehouses and freight carriers, which many pharma companies use for distribution. Notably, there is a Wholesaler Distribution module (suite bundle) that helps pharma distributors comply with DSCSA by automating verification of returned products via a Verification Router Service before resale linkedin.com. In short, the order/procurement modules ensure materials and products flow smoothly while maintaining compliance checks at each step (e.g. blocking shipment of any lot that’s on quality hold or missing DSCSA verification).
Manufacturing (Production Management)
NetSuite’s manufacturing module enables labs to plan and execute production of batches or assemblies. Users can define Bills of Materials (BOMs) or formulas for drug products, create work orders for batch runs, and track production status and yields. The system supports production planning and scheduling to balance resource supply and demand, and it allows defining routing steps with standard times, so labs can schedule work centers and labor. In a pharma context, each work order represents a batch record – capturing components issued (with lot numbers), processing steps, and outputs. NetSuite’s base manufacturing functionality ensures that production processes are controlled and documented in compliance with GMP standards sikich.com. Key features include tracking work-in-progress, capturing lot numbers of consumed ingredients, and recording completion of each batch with a us) and can enforce FEFO (first-expiry-first-out) allocation to reduce expired inventory. Validating the inventory module is crucial for FDA-regulated labs – it confirms that inventory records are accurate and that the system supports full traceability from raw materials to finished goods sikich.com. Key inventory capabilities include real-time stock levels, warehouse management (bins, picking/putaway), and integration of inventory status with quality control (for example, materials can be put on quality hold until QC tests pass). NetSuite’s lot traceability features help maintain compliance by ensuring that for any given drug batch, you can quickly find all related transactions (where used, which orders shipped) – a cornerstone of product safety and recall readiness linkedin.com.
Order Management & Supply Chain
NetSuite’s order management module covers the order-to-cash and procure-to-pay cycles, tying together customer orders, procurement of materials, and fulfillment. For a pharma lab, this means sales orders for products (or internal demand for clinical trial materials) are seamlessly linked to inventory availability and production plans, while purchase orders for raw chemicals, APIs, or lab supplies are managed in the same system. The module ensures efficient and controlled purchasing processes – including vendor management, purchase order processing, receiving inspections, and distribution logistics sikich.com. Supplier qualification can be tracked (via vendor records and custom fields/workflows) to ensure materials are sourced from approved vendors, a GMP requirement. NetSuite can automatically reserve inventory for orders, generate pick/pack/ship tasks, and handle shipping documentation which is important if distributing controlled substances or temperature-sensitive products. On the procurement side, it maintains a complete audit trail of each lot received (linking to COA documents from vendors) and can enforce two-way or three-way match for quality and financial control. Validating supply chain functions is important to confirm compliance – it reduces risk of supply chain disruptions and ensures all steps (from supplier to customer) meet FDA quality and record-keeping requirements sikich.com sikich.com. NetSuite also supports integration with 3PL warehouses and freight carriers, which many pharma companies use for distribution. Notably, there is a Wholesaler Distribution module (suite bundle) that helps pharma distributors comply with DSCSA by automating verification of returned products via a Verification Router Service before resale linkedin.com. In short, the order/procurement modules ensure materials and products flow smoothly while maintaining compliance checks at each step (e.g. blocking shipment of any lot that’s on quality hold or missing DSCSA verification).
Manufacturing (Production Management)
NetSuite’s manufacturing module enables labs to plan and execute production of batches or assemblies. Users can define Bills of Materials (BOMs) or formulas for drug products, create work orders for batch runs, and track production status and yields. The system supports production planning and scheduling to balance resource supply and demand, and it allows defining routing steps with standard times, so labs can schedule work centers and labor. In a pharma context, each work order represents a batch record – capturing components issued (with lot numbers), processing steps, and outputs. NetSuite’s base manufacturing functionality ensures that production processes are controlled and documented in compliance with GMP standards sikich.com. Key features include tracking work-in-progress, capturing lot numbers of consumed ingredients, and recording completion of each batch with a unique lot or serial number. The module can also log equipment usage and maintenance status (e.g. ensuring equipment calibration is up-to-date before use, per GMP requirements sikich.com). While basic NetSuite manufacturing provides core capabilities, many pharma labs extend this with Advanced Manufacturing (covered in the next section) for more complex scheduling, batch tracking and data capture. Nonetheless, even out-of-the-box, NetSuite supports critical needs like batch/lot traceability, electronic routing instructions, and quality checks at production steps, either through native features or light customizations intuitionlabs.ai. Validating the manufacturing module is a priority for FDA-regulated companies to ensure all production activities (materials, processes, signatures) are reliably recorded in the ERP sikich.com.
Quality Management and CRM (Complaints)
While quality management is treated in detail as an industry-specific solution below, it’s worth noting that NetSuite’s core platform can track certain quality processes. For example, NetSuite includes a Customer Relationship Management (CRM) module that labs can use to record customer feedback or product complaints, linking them to batches or lot numbers. In FDA-regulated environments, complaint handling and adverse event reporting must be documented and investigated. NetSuite’s CRM can be configured to manage complaint cases, trigger investigations, and link to corrective/preventive actions. Validating the CRM module ensures the system can support effective documentation of complaints and traceability of customer interactions sikich.com. This integration of CRM with ERP means that a field-reported issue (say, a stability problem with a drug batch) can be tied directly to manufacturing and quality records in NetSuite. The platform also natively supports return merchandise authorization (RMA) processes, which a pharma company might use to manage returns or recalls of suspect product, again linking to lot numbers. In summary, NetSuite’s core modules (financials, inventory, orders, manufacturing, and CRM) provide a foundation for running a pharma lab’s operations with compliance in mind. Next, we delve into additional modules and bundles tailored to industry-specific needs like formal quality control and regulatory compliance.
Industry-Specific Modules & SuiteApps for Pharma
Pharmaceutical manufacturers often require functionality beyond standard ERP to meet industry regulations and best practices. NetSuite addresses this through specialized modules (some native, some as SuiteApps – add-on applications) and pre-configured industry solutions. Key industry-specific extensions include Quality Management, Compliance/Regulatory Management, and Batch Record control. NetSuite’s SuiteSuccess for Life Sciences is an example of a pre-configured solution that delivers pharma best practices (pre-set roles, workflows and reports aligned to FDA compliance and clinical processes) right out of the box intuitionlabs.ai. Additionally, partners like AdaptaLogix (now part of BDO Digital) have created pharma-specific bundles – BDO offers a “21 CFR Part 11 GMP compliant solution” built on NetSuite to meet the unique needs of biotech and pharma firms bdo.com. Below are important pharma-focused modules and solutions:
Quality Management (QMS) Module
Maintaining product quality is paramount in pharma. NetSuite offers a Quality Management module (available as a SuiteApp) that formalizes and automates quality processes within the ERP. This module allows companies to define quality test plans, inspection criteria, sampling procedures, and to record results for inspections on incoming materials, in-process checks, and finished goods. For example, a lab can set up a quality inspection requirement for each received lot of a raw material – NetSuite will prompt inspectors to input test results (e.g. assay purity, microbial count) and can prevent the lot from being used until tests pass. The quality module supports tracking of non-conformances (NC) and deviations, with workflows for review and disposition (e.g. scrapping a failed batch or issuing a deviation report). It also includes Corrective and Preventive Actions (CAPA) management: if a trend of deviations is found, a CAPA record can be initiated, assigned to responsible owners, and tracked to closure – all within NetSuite. Other elements typically encompassed in a pharma QMS, such as change control, document control, training records, and supplier qualification, can be managed either through NetSuite’s quality module or through extensions. NetSuite’s quality capabilities are integrated with inventory and production data, meaning a quality hold can automatically prevent a specific lot from being allocated to orders or production until the issue is resolved intuitionlabs.ai intuitionlabs.ai. This integration ensures only quality-released materials proceed through the supply chain. In fact, NetSuite’s built-in quality module includes functionality for NC/CAPA, audit management, document approvals, training tracking, and approved supplier lists – all within the ERP linkedin.com. For companies that require more extensive quality systems (for example, tracking equipment calibration schedules, electronic logbooks, or environmental monitoring), the NetSuite ecosystem offers third-party SuiteApps such as Quality for NetSuite by uniPoint, which provides 25+ quality sub-modules running inside NetSuite intuitionlabs.ai. Deploying an eQMS SuiteApp like uniPoint can turn NetSuite into a full-fledged quality management system (covering complaints, audits, calibration, etc.) without needing a separate platform intuitionlabs.ai. Whether using NetSuite’s native quality features or an extended SuiteApp, pharma labs can ensure that all quality data (test results, deviations, CAPAs) reside in the same system as production and inventory data. This single-source-of-truth approach simplifies compliance: when auditors ask for evidence of quality control, all records – from batch test results to investigation reports – can be pulled directly from NetSuite with full traceability intuitionlabs.ai.
Compliance Management & Regulatory Reporting
Pharmaceutical firms must comply with a host of regulatory reporting requirements and maintain diligent records for inspections. NetSuite doesn’t have a module labeled “compliance management” per se, but it provides tools and templates to manage compliance tasks and generate required documentation. For instance, NetSuite’s Regulatory Compliance SuiteApp (often part of pharma implementations) can assist with compiling data for FDA submissions and tracking regulatory obligations. NetSuite can produce or store reports for: batch production records, Certificates of Analysis (COAs), Annual Product Reviews (APR), stability studies, and more. The system can be configured with workflows for reviewing and approving these documents electronically (with e-signatures). Additionally, NetSuite provides pre-built workflows and templates for common FDA reports such as Adverse Event Reports (AER) for pharmacovigilance, product complaint forms, and even supports electronic submission formats linkedin.com. For example, a lab could record a product complaint in NetSuite and use a workflow to ensure an investigation is conducted and an FDA MedWatch Form 3500A is generated if the complaint is deemed reportable – all steps tracked in the ERP. NetSuite’s audit trail and electronic signature features (detailed in the compliance section later) also fall under compliance management, ensuring that any changes to records or critical actions are logged and approved. The Sikich validation guide identifies Compliance Reporting, Audit Trail Management, Electronic Signatures, and Regulatory Submissions as key areas to address for an ERP in FDA-regulated industries sikich.com. NetSuite meets these needs with its built-in capabilities: every transaction and master record has a viewable change log, reports can be designed to show compliance metrics (like deviations per batch or on-time reporting), and integrations can be made with specialized regulatory systems. In some cases, companies integrate a Regulatory Information Management (RIM) system (such as Veeva Vault RIM) with NetSuite to sync data on product registrations, lot release, and distribution for compliance with rules like DSCSA or international health authority filings intuitionlabs.ai. NetSuite’s role-based access and workflow engine ensure that required reviews (for example, QA approval of a batch record, or CFO sign-off on financial disclosures like SOX 404) happen before any critical process is marked complete. In summary, NetSuite provides a solid foundation for compliance management by combining recordkeeping, workflow, and reporting tools, and it can be extended or integrated with niche compliance software when necessary.
Batch Record Control (Electronic Batch Records)
Accurate batch records are the heartbeat of pharmaceutical manufacturing compliance. Traditionally, batch production records were paper-based, but labs are increasingly moving to Electronic Batch Records (EBR) for efficiency and data integrity. NetSuite supports batch record control in two primary ways: through its core transaction records (work orders, production records, quality tests attached) and through the Advanced Manufacturing module which fully enables EBR functionality. Each work order in NetSuite can serve as a master batch record (MBR) template, listing the materials, equipment, and processing steps required. As production is executed, NetSuite captures actual data: which lots of raw materials were consumed, who performed each step, start/end times, yields, and any deviations or incidents noted. With Advanced Manufacturing (discussed next), NetSuite can enforce the process steps so that operators must complete predefined steps in sequence and input data (or scan barcodes) at each step, effectively creating a real-time electronic batch record linkedin.com linkedin.com. The system can be configured such that if a critical quality check is missing or out-of-spec data is entered, the workflow will halt and require supervisor intervention – this prevents incomplete or non-compliant batch records. Electronic signatures can be required at key points (for example, supervisor verification of ingredient addition or QA approval at batch completion), meeting FDA’s requirements for signed batch documentation. NetSuite’s capability to attach files to records also means supporting documents like equipment printouts, deviation reports, or lab test results (perhaps coming from a LIMS) can be linked directly to the batch record. By having all batch data in one system, review and release of batches become much more efficient – QA can review an electronic record with audit trails rather than shuffling paper. Overall, NetSuite provides the tools to implement rigorous batch record control: predefined recipes, controlled electronic workflows, automatic data capture, and secure recordkeeping. This satisfies the FDA’s 21 CFR Part 211 requirements for production and control records for drug manufacturing, and it greatly reduces errors compared to manual record-keeping linkedin.com linkedin.com. Many pharma companies use NetSuite’s EBR capabilities to speed up batch release and ensure nothing is missed in the documentation. (It’s worth noting that if a company has an existing standalone MES/EBR system, it can integrate with NetSuite – but a benefit of NetSuite is that advanced manufacturing and quality modules can remove the need for a separate EBR system by handling it natively within the ERP.)
NetSuite Advanced Manufacturing for GMP Compliance
NetSuite Advanced Manufacturing is an add-on module (SuiteApp) that significantly enhances the manufacturing capabilities of NetSuite, and it is particularly valuable for pharma labs operating under GMP conditions. Advanced Manufacturing provides a dedicated Manufacturing Work Bench interface and additional tools to manage complex production processes. With this module, manufacturers can define detailed work instructions and routings for each operation, associate specific materials and labor to each step, and set up quality check prompts at the appropriate points docs.oracle.com. For a GMP-compliant environment, Advanced Manufacturing enables enforcement of procedures: it will not allow operators to skip required steps or proceed without entering data or obtaining the necessary sign-offs linkedin.com. This level of control is crucial for compliance, ensuring that every batch follows the approved Master Batch Record to the letter.
One of the standout features of Advanced Manufacturing in pharma is its support for automated data capture and Electronic Batch Records (EBR). As operators work through a batch, they can use a tablet or kiosk interface to record each action (or even scan barcoded lot numbers and equipment IDs), and the system automatically timestamps and logs the activity linkedin.com. All material consumptions, equipment usage, and in-process test results get recorded in real time, building the batch record incrementally as work is performed. For example, when adding an ingredient, the operator can scan the ingredient’s lot, and NetSuite will verify it’s the correct item and within its potency period, then log the quantity used. If a step requires a temperature check or pH reading, the operator must input that result (or it could even interface with IoT sensors to auto-record it). By the end of the batch, you have a complete electronic record with all process data, significantly reducing the chance of omissions or transcription errors compared to paper records linkedin.com linkedin.com. This not only improves compliance (since regulators expect accurate, contemporaneous records) but also speeds up batch review and release – QA can review the electronic log and sign off much faster.
Advanced Manufacturing also brings finite scheduling and capacity planning tools that are valuable for scaling production. Labs can account for equipment downtime, cleaning time, and other constraints when scheduling batches docs.oracle.com. The system helps optimize the production schedule to meet demand while respecting those constraints (e.g., not scheduling two incompatible products in the same suite back-to-back without cleaning). It also introduces shop floor control features: supervisors can monitor the progress of each batch in real time, and production managers get dashboards for throughput, yield, and efficiency metrics.
From a GMP compliance perspective, Advanced Manufacturing ensures process consistency and control. It integrates with NetSuite’s quality and inventory modules, so if a quality test fails, the system can halt further processing of that batch. It can also interface with equipment or control systems – for instance, connecting to a weighing scale to automatically record actual weighed quantities, or to a manufacturing execution device. This kind of integration can make the ERP part of the direct production control system, which then requires rigorous validation but pays dividends in compliance. Speaking of validation, all these features of Advanced Manufacturing are designed to be fully validated in a regulated environment: every configuration (such as a change to a routing or a quality checkpoint) can be documented and tested.
In summary, NetSuite Advanced Manufacturing extends the ERP into a true Manufacturing Execution System (MES) layer, tailored for regulated production. It enables pharmaceutical labs to automate batch processes, enforce GMP procedures, capture complete electronic batch records, and improve production efficiency – all while staying compliant. By using Advanced Manufacturing, companies can confidently move away from paper batch records, knowing that NetSuite will capture who did what, when, with which materials, producing an audit-trailed batch history that stands up to FDA inspection.
Compliance and Regulatory Support (FDA 21 CFR Part 11, GxP, etc.)
Running an ERP in a pharmaceutical environment demands that the system itself comply with certain regulatory expectations. NetSuite is often described as “21 CFR Part 11 ready” – it includes the technical features needed for compliance with FDA’s electronic records and electronic signatures rule intuitionlabs.ai. However, companies must still configure and use these features properly and perform computer system validation (CSV) to confirm the system’s fitness for use. This section outlines how NetSuite supports FDA 21 CFR Part 11, broader GxP requirements (such as GMP), and other U.S. regulations.
21 CFR Part 11 (Electronic Records & Signatures): Part 11 sets requirements to ensure that electronic records and signatures are trustworthy and equivalent to paper records. NetSuite has robust, built-in functionality to facilitate Part 11 compliance out of the box linkedin.com. Key features include:
-
Audit Trails: NetSuite automatically maintains an immutable, time-stamped audit log of all changes to records (creation, edits, deletions) along with the user ID and timestamp linkedin.com. This audit trail cannot be modified by end users, satisfying the requirement for secure, computer-generated audit trails. Auditors can review who changed what and when, for any regulated record (e.g. an inventory adjustment, a quality test result, a user permission change).
-
Data Integrity Controls: All records are stored with system-enforced version control and cannot be overwritten without leaving a trace. NetSuite can be configured to require a reason (comment) for critical data changes. The system also prevents unauthorized deletions – for example, you cannot simply delete a transaction that’s been processed; if voided or adjusted, it’s logged linkedin.com. These controls align with FDA’s data integrity guidance and ALCOA+ principles (data should be Attributable, Legible, Contemporaneous, Original, Accurate, etc.).
-
User Access & Security: NetSuite uses role-based access control. Administrators can set granular permissions so users only see and edit what they should. It supports password policies, multi-factor authentication, and automatic session timeouts to enhance security linkedin.com. For Part 11, this helps ensure that only authorized individuals can use the system functions, and unique user accounts prevent credential sharing.
-
Electronic Signatures: NetSuite’s platform includes the ability to capture electronic signatures for approvals. This typically involves re-entering login credentials or a signature PIN and recording the meaning of the signature (e.g. “Approved” or reason for approval) whenever a user signs a record or transaction. NetSuite allows configuring e-signature requirements on any record or workflow step that needs formal approval linkedin.com. These signatures are then bound to the electronic record and become part of the audit trail, meeting FDA’s criteria for electronic signatures (unique, password-protected, signature manifestations). For example, you could require an e-signature by a QA manager to authorize batch disposition, or a QC analyst’s signature when entering test results. NetSuite fully supports the implementation of these Part 11-compliant e-signatures with built-in functionality linkedin.com.
GxP and System Validation: GxP refers to Good Practices (GMP – Manufacturing, GLP – Lab, GCP – Clinical, etc.). A common requirement across GxP is that computerized systems be validated (as per guidelines like FDA’s guidance or ISO 13485, and GAMP5 framework). NetSuite, being a cloud-based system with continuous updates, may raise the question: can it be validated? The answer is yes – NetSuite is a fully validatable cloud platform, and hundreds of life sciences companies have successfully validated it for GxP use linkedin.com. Oracle provides documentation and support to ease this process, including vendor-supplied validation templates. For example, NetSuite can provide template IQ/OQ test scripts, traceability matrices, and validation plan documents aligned with GAMP5 guidelines linkedin.com linkedin.com. This means a lab doesn’t have to start from scratch in writing test cases for every module – you can leverage pre-written scripts for standard functionality and then add cases for any custom configurations. NetSuite’s development processes and biannual release upgrades follow a controlled procedure with extensive internal testing, and Oracle provides release validation kits that document what changed and any impact on regulated features linkedin.com. Companies are still responsible for performing their own validation, but this vendor support significantly reduces effort. Additionally, NetSuite’s SuiteCloud platform (for customizations) is designed to maintain segregation of custom code vs. core code, and it offers version control for scripts and configurations linkedin.com. This helps in change control – for instance, if you create a custom workflow for electronic signatures, you can document and test that as a separate item without worrying about Oracle’s base code. Many firms also use third-party validation management tools (like ValGenesis or USDM’s Cloud Assurance) to automate NetSuite validation and change management intuitionlabs.ai. The key point is that NetSuite can be validated to satisfy FDA’s requirements; once validated, procedures must be in place to keep it in a validated state (monitoring changes, periodic reviews, etc., which are often facilitated by the compliance and validation accelerators mentioned).
Other Regulatory Requirements: Beyond Part 11 and general GMP, U.S. pharma labs face additional regulations that NetSuite helps address:
-
21 CFR Parts 210/211 (cGMP for Drug Manufacturing): These require thorough documentation of production and quality control. As described earlier, NetSuite’s batch records, quality modules, and inventory traceability help ensure compliance with these regulations by maintaining required production and control records and distribution histories sikich.com sikich.com.
-
21 CFR Part 820 (Quality System Regulation for medical devices): For companies involved in combination products or devices, NetSuite’s quality and document control features can support Part 820 requirements as well (for example, design history file tracking via custom records, complaint handling, etc.). Sikich notes that many of the same NetSuite modules (inventory, production, QA, etc.) are relevant to validating compliance for both pharma GMP and device QSR sikich.com sikich.com.
-
DSCSA (Drug Supply Chain Security Act): This U.S. law mandates serialization and traceability for prescription drugs. NetSuite’s serialization and lot tracking capabilities enable compliance with unit-level tracking. Furthermore, NetSuite can integrate with serialization systems (like TraceLink or SAP ATTP) or handle certain aspects internally. For example, NetSuite’s Wholesaler VRS integration (Verification Router Service) allows distributors to verify returned product identifiers against manufacturer data linkedin.com. NetSuite also keeps the full distribution history of each lot/serial, which can be used to quickly respond to trace requests from the FDA or trading partners.
-
Environmental, Health & Safety (EHS): While not a core focus of NetSuite, companies can track hazardous materials inventory in NetSuite and integrate with EHS systems for reporting to EPA or OSHA. If the lab deals with controlled substances, DEA compliance (ARCOS reporting, etc.) can be facilitated by capturing required data in NetSuite and then extracting it for submission.
-
HIPAA: If the pharmaceutical operation handles any patient health information (for example, in a pharma lab doing clinical diagnostics or patient-specific cell/gene therapies), NetSuite can be configured to meet HIPAA security requirements. Oracle offers a HIPAA-compliant environment for NetSuite (upon request, with a Business Associate Agreement), ensuring data encryption and security controls align with healthcare privacy laws intuitionlabs.ai intuitionlabs.ai.
-
SOX (Sarbanes-Oxley Act): For publicly traded pharma companies, NetSuite’s internal controls (workflow approvals, audit logs, segregation of duties via roles) support SOX compliance. It’s worth noting that NetSuite has been audited for SOC1, and by using its features properly, companies can satisfy SOX 302 and 404 requirements for financial reporting controls intuitionlabs.ai. Many firms supplement NetSuite with period-close management tools like BlackLine for account reconciliations intuitionlabs.ai, but NetSuite provides the transactional integrity and permission controls underlying those processes.
In essence, NetSuite offers a strong compliance foundation for U.S. pharma requirements. It addresses electronic records rules, supports validated state operations, and provides the traceability needed for GMP. Companies do need to implement proper SOPs and maintain validation, but the software capabilities are there. The result is an ERP system that can pass FDA audits and help avoid the data integrity pitfalls that have led to warning letters for others (notably, ~80% of recent FDA observations relate to data integrity failures – something robust systems aim to prevent intuitionlabs.ai intuitionlabs.ai).
Integrations: LIMS, MES, and Validation Tools
No system operates in a vacuum – pharmaceutical labs often have a larger IT ecosystem that NetSuite needs to fit into. The good news is that NetSuite is an open platform (with web services, APIs, and integration tools) that can connect to various specialized systems. Key recommended integrations for a pharma manufacturing lab include Laboratory Information Management Systems (LIMS), Manufacturing Execution Systems (MES), and validation/quality tools:
-
Laboratory Information Management System (LIMS): A LIMS manages detailed laboratory data – test results, sample tracking, method protocols, instrument data – which is crucial for product release and stability programs. Integrating NetSuite with a LIMS ensures that quality control results flow into the ERP. For example, when QC tests a batch of tablets for dissolution and potency, the LIMS can push the approved results and perhaps a Certificate of Analysis into NetSuite, which in turn can automatically update the batch record status to “approved for release.” A LIMS integration feeds test results and certificate data into NetSuite, tying QC results directly to batch records in the ERP intuitionlabs.ai. This eliminates double data entry and ensures that anyone looking at a batch in NetSuite can see its lab results and whether it passed all specs. Many labs use commercial LIMS like LabWare, SampleManager, or newer cloud LIMS (Benchling, QBench, etc.) – these can be integrated via API or flat-file imports. The integration typically involves mapping the LIMS sample ID or lot number to the NetSuite item lot record, so the systems speak the same language. With a proper LIMS-ERP integration, quality release becomes streamlined: as soon as the LIMS marks tests as passed, NetSuite can mark the inventory as released and even trigger a notification to the supply chain team that the batch is ready to ship.
-
Manufacturing Execution System (MES): Some pharmaceutical manufacturers, especially larger ones or those with complex continuous processes, might use a dedicated MES for real-time shop floor control. An MES can handle equipment interfaces, real-time process parameter monitoring, and detailed production scheduling beyond the scope of an ERP. NetSuite’s own Advanced Manufacturing module covers many MES-like functions (and NetSuite has a lightweight native “MES” functionality for shop floor data entry on tablets), but if a company has an existing MES (like Siemens Opcenter, Rockwell FactoryTalk, or a home-grown solution), integration is beneficial. MES-ERP integration allows coordination of production activity with supply chain management, inventory, sales, and customer service netsuite.com. Practically, this means the MES can send production results to NetSuite (e.g. confirming that a batch was produced with X yield and consuming Y raw material lots), and NetSuite can send master data to MES (e.g. production orders, BOMs, inventory levels). This keeps inventory and financials in sync with what’s happening on the factory floor. For example, if a batch is completed in the MES, it can trigger NetSuite to automatically receive the finished goods into inventory and decrement the raw materials – maintaining accurate books. Additionally, if the MES detects deviations or events on the line, those could be flagged in NetSuite for QA action. Integrating an MES can also offload some detailed execution data to the MES while NetSuite focuses on transactional records and planning. The result is a harmonized system: NetSuite as the planning and inventory backbone, MES as the execution engine, each doing what it does best but sharing data to avoid disconnects. It’s important to note that integrating MES (or any shop floor system) with an ERP like NetSuite must be done carefully under change control and will itself require validation to ensure data flows are correct in a GxP environment intuitionlabs.ai.
-
Third-Party Validation and Quality Tools: To augment NetSuite’s compliance capabilities, companies often leverage specialized software for managing the validation and quality process. These aren’t integrations in the transactional sense, but they work alongside NetSuite. For example, validation lifecycle management tools like ValGenesis or Kneat are used to manage computer system validation documentation – they can import NetSuite requirements/configurations and provide a platform to author and execute test scripts, track defects, and maintain a live traceability matrix intuitionlabs.ai. While NetSuite handles the business process data, a tool like ValGenesis ensures that any change to the NetSuite configuration (like a new custom script or an update to a workflow) goes through proper testing and approval in a controlled way intuitionlabs.ai. Some consulting firms (e.g. USDM) provide “validated cloud” packages or continuous validation services that connect with NetSuite’s updates, ensuring that when Oracle issues a new release, regression tests are executed and documented. These tools/services don’t directly push data into NetSuite’s UI, but they often pull metadata from NetSuite (like a list of custom objects or transactions) to use in validation test cases. In the broader quality domain, companies might integrate electronic Document Management Systems (eDMS) or Electronic Quality Management Systems (eQMS) if they prefer to use those for document control, training, CAPA, etc., instead of or in addition to NetSuite. Solutions like Veeva QualityDocs, MasterControl, or Qualio can be used to manage controlled documents (SOPs, batch record templates) and training records, while NetSuite focuses on execution records. There are known cases where pharma companies integrate Veeva with NetSuite so that master data (item codes, specs) and certain transactional events (like a lot release or deviation) sync between the two systems intuitionlabs.ai intuitionlabs.ai. Similarly, Greenlight Guru or other QMS platforms might be connected to push/pull quality event data. However, as mentioned earlier, some choose to avoid external QMS by using NetSuite-based solutions (SuiteApps) to keep everything in one system intuitionlabs.ai. Whether the QMS is internal or external, the integration focus is on data consistency – for example, if a CAPA is initiated in an external QMS, linking it to the relevant lot or product in NetSuite ensures that anyone looking at that product record in ERP can be aware of open quality issues.
In addition to the above, other integrations worth noting include Learning Management Systems (LMS) for tracking GMP training (which can link to NetSuite employee records) intuitionlabs.ai, and specialized traceability networks (like connecting NetSuite with FDA’s electronic Drug Registration and Listing System for automatic updates, or connecting to trading partner networks for supply chain reporting). There are also financial close tools (BlackLine, FloQast) and governance, risk & compliance (GRC) analytics integrations intuitionlabs.ai, but those are more about corporate compliance than lab operations.
Overall, integrating NetSuite with LIMS, MES, and validation/QMS tools results in a more holistic IT ecosystem. Data flows between lab instruments, execution systems, and the ERP mean fewer manual entries and fewer discrepancies. This integrated approach is highly recommended: it reduces errors (no need to type results from LIMS into ERP by hand), improves compliance visibility (quality and production data in one dashboard), and simplifies audits since all systems are aligned intuitionlabs.ai intuitionlabs.ai. Pharma labs should plan their NetSuite implementation as part of a broader digital landscape, ensuring the ERP is the backbone that connects to the right specialized systems to cover all regulatory and operational needs.
Scalability for Labs of All Sizes
One of the advantages of NetSuite is its scalability – it can support a small biotech lab with a handful of users and one site, and grow all the way to a large enterprise with multiple plants and global operations. For small to mid-sized labs, NetSuite’s cloud-based SaaS model is appealing because it avoids heavy IT overhead and can be deployed relatively quickly. These organizations often have limited IT staff and need a system that “just works” out of the box. NetSuite fits that bill, providing core functionality via SuiteSuccess industry configurations, which reduces implementation time. Many emerging biotech and pharma companies have chosen NetSuite early on because they can get up and running in months, not years intuitionlabs.ai intuitionlabs.ai. For example, NetSuite’s rapid deployment allowed a clinical-stage company to implement ERP and replace spreadsheet-based processes before a critical trial or product launch timeline intuitionlabs.ai. The system’s automatic upgrades (twice yearly) ensure that even a small company is always on the latest version, without needing a dedicated team to perform updates – a significant benefit when resources are constrained intuitionlabs.ai.
As a company grows, NetSuite scales seamlessly in user count and transaction volume. You can start with just the financials and inventory for a single lab, then activate additional modules (manufacturing, quality, CRM, etc.) or add users as needs expand. There’s no need to “re-platform” as you would if outgrowing a basic accounting system – NetSuite’s single codebase handles from startup to enterprise. In fact, NetSuite has noted that a large share of tech and life science IPOs have been on NetSuite, demonstrating that companies can go from inception to IPO on the same system intuitionlabs.ai. NetSuite’s architecture can handle hundreds of users and multi-subsidiary setups. For large enterprises or multi-site pharma companies, NetSuite OneWorld provides capabilities to manage multiple manufacturing facilities, distribution centers, and legal entities within one account. Each subsidiary can have its own base currency, taxation rules, and compliance reporting, while rolling up financials to a corporate parent – useful for a global pharma with operations in the US, EU, etc. linkedin.com. BioMonde, for instance, is a biotech that expanded internationally and leveraged NetSuite OneWorld to manage complex multi-country operations (manufacturing and distribution across several countries) with a unified data model intuitionlabs.ai intuitionlabs.ai. The CFO of BioMonde highlighted that NetSuite’s unified platform gave them a 360° real-time view of finances, customers, products and orders across all locations, which helped them scale into new markets while maintaining quality and compliance oversight intuitionlabs.ai.
NetSuite’s cloud infrastructure (now under Oracle) can scale in terms of performance as well – it dynamically adjusts to handle increased transaction loads, larger data sets (like years of batch records), and more complex reporting. If a lab grows into a commercial manufacturer shipping thousands of orders, NetSuite can accommodate that throughput. For very large enterprises (e.g., Big Pharma with tens of thousands of users), NetSuite might not replace a Tier 1 ERP like SAP for all purposes, but it can still play a role in subsidiaries or specific divisions. That said, NetSuite’s “one platform” strategy means a company doesn’t have to switch systems as they grow – many pharma companies have proven you can scale through commercialization and even post-IPO on NetSuite intuitionlabs.ai.
Another aspect of scalability is adding functionality as the company’s needs broaden. A small R&D lab might initially not need a manufacturing module or advanced quality module. As it begins pilot production or enters commercialization, it can enable those modules or integrate new systems. NetSuite’s modular licensing allows adding capabilities when required (for instance, implementing Advanced Manufacturing when you move from manual processes to a more automated production line). This pay-as-you-grow approach ensures scalability of cost as well – you’re not forced to invest in features until you’re ready to use them intuitionlabs.ai.
Finally, scalability isn’t just technology – it’s also about compliance as you grow. NetSuite aids this by supporting stringent compliance at scale. As an organization expands, maintaining compliance across more users and sites is challenging. NetSuite’s centralized control (user roles, workflows, audit trail) and ability to handle multi-site data in one system means compliance processes can be standardized and monitored globally. For example, a corporate quality team can run a single report in NetSuite to see all deviations across all plants, or ensure every site is following the same SOPs embedded in the ERP. This can be a huge advantage over having disparate systems in each facility.
In summary, NetSuite is well-suited for small and mid-sized pharma labs, and it has the capabilities to grow with the organization into a large enterprise with complex operations. Its cloud nature, OneWorld multi-entity support, and modular growth path provide flexibility. Many pharma companies have demonstrated successful scaling on NetSuite – from startups focusing on science to mature companies managing global supply chains on the platform.
Customization and Automation Capabilities
Every pharmaceutical operation has unique elements – whether it’s proprietary processes, specialized calculations (like yield potency adjustments), or specific compliance workflows. NetSuite recognizes this by providing robust customization and automation tools, collectively known as the SuiteCloud Platform. For pharma labs, this means the ERP can be tailored to fit your exact business processes while still maintaining compliance (with proper change control). Here are the key ways NetSuite can be customized and automated:
-
SuiteBuilder (Configuration): Many customizations in NetSuite can be done via point-and-click. You can add custom fields to capture data specific to pharma (for instance, an assay result field on a lot record, or a flag for DEA Schedule on an item). You can create custom record types to track things like stability studies or equipment logs, and link them to standard records. Forms and layouts can be configured so that users see fields and terminology familiar to them (e.g., renaming “Assembly Item” to “Formulation” for clarity). These configurations do not require coding and can be carried out by a NetSuite administrator. They are also preserved through upgrades, but in a validated environment, they should be assessed and tested when changed.
-
SuiteScript (Custom Coding): For more complex needs, NetSuite allows adding custom business logic using SuiteScript (JavaScript-based scripting API). In a pharma lab, SuiteScript could be used to implement custom validations or calculations – for example, automatically calculating potency-adjusted quantities to dispense based on an assay purity result, or enforcing that certain fields are populated before a record can be saved (like requiring a deviation number if a result is out-of-spec). Scripts can also perform actions like integration with external systems (though often SuiteTalk web services or integration platforms are used for that). An example use case: if a manufacturing batch fails a criteria, a script could automatically create a Non-Conformance record and alert the quality team. NetSuite’s SuiteScript is powerful and can access practically all records and transactions. From a compliance standpoint, any custom scripts need to be documented and validated (they essentially become part of your computerized system landscape), but NetSuite aids this by supporting script versioning and sandbox testing linkedin.com. With proper development lifecycle (e.g., using a sandbox account for testing and then deploying via SuiteCloud Change Sets), changes can be managed systematically.
-
SuiteFlow (Workflow Engine): SuiteFlow is a graphical workflow tool that allows automation of business processes without coding. This is extremely useful in regulated environments to ensure nothing falls through the cracks. Using drag-and-drop, you can create workflows for things like: routing a new vendor through a quality approval process, automating the approval of a purchase requisition, or orchestrating the steps of a change control process. For example, a change request for a manufacturing process can be initiated as a custom record in NetSuite; SuiteFlow will then automatically route it to the relevant Regulatory Affairs manager and Quality Assurance manager for approval (with e-signatures) before allowing the change to be implemented linkedin.com linkedin.com. If someone tries to implement the change without approval, the workflow can block it. Another example: when a new batch production is completed, a workflow could send a notification to QA to perform the review, and even generate a draft Certificate of Analysis. The beauty of SuiteFlow is that it’s relatively easy to maintain (by admin or developer) and can enforce multi-step procedures that are critical in pharma. Automated workflows not only reduce manual effort but also improve consistency and traceability – every approval or action is logged by the system, and you can report on process performance (e.g., how long each approval takes) to identify bottlenecks linkedin.com linkedin.com.
-
SuiteAnalytics (Reporting and Dashboards): While not a customization in the sense of altering functionality, the ability to create custom reports and saved searches is worth mentioning. Pharma users can create tailored reports, such as a Deviation Trend report, a Batch Genealogy report (which raw material lots went into which batches and where they were shipped), or a regulatory compliance dashboard showing KPIs like “Lots pending QA release” or “Open CAPAs by category”. These can be done with NetSuite’s built-in tools, often without any programming – just by defining search criteria and results. SuiteAnalytics also supports more advanced pivot-type workbook analyses and can embed charts. This empowers teams to monitor compliance and operations proactively linkedin.com linkedin.com. For instance, a quality manager might have a dashboard with a tile showing “Batches pending APR review” and “Training past due for lab employees” (if training records are tracked). The system’s ability to drill-down means one can click a metric and get to the underlying records immediately linkedin.com.
-
Integration (SuiteTalk and RESTlets): If needed, custom integration logic can be written via SuiteTalk SOAP/REST web services or custom RESTlet scripts. This is how NetSuite can communicate with external instruments or databases in a bespoke way if out-of-the-box connectors are not available. For example, a custom RESTlet could allow a lab instrument software to send its results directly to NetSuite (bypassing a LIMS if not used). Many companies use integration platforms (like Boomi, MuleSoft) with NetSuite connectors to reduce custom code for integrations, but in some cases, direct scripting is useful for niche integrations.
Crucially, NetSuite’s customization framework is designed to let you extend the system without breaking the core. Custom objects and scripts coexist with standard functionality, and Oracle’s upgrades won’t overwrite your customizations (unless an API changes, which is rare and managed). For validated environments, this means you can add functionality while keeping the core validated state intact. Of course, any customization must go through change control and possibly additional validation. NetSuite’s support for multiple development environments (production, sandbox, etc.) allows you to test changes safely before rolling them out – which aligns with FDA’s expectations that system changes are documented and tested. As noted in a LinkedIn report, the flexibility of SuiteCloud lets pharma companies build and validate custom workflows and reports without compromising the core system’s validation status, especially if they leverage the proper tools for script versioning and release management linkedin.com.
In summary, NetSuite provides high configurability to adapt to a pharma lab’s needs and automation capabilities to eliminate manual steps. You can tailor the ERP to handle your specific formulations, quality flows, and reporting needs rather than having to fit your processes to a rigid system. Many pharma firms have taken advantage of this – for example, configuring NetSuite to calculate theoretical vs. actual yield and flag if yield deviation exceeds a threshold, or automating the creation of stability study records when a new batch is produced. The combination of customization and automation ensures that NetSuite not only fits the business on day one, but can evolve as the lab’s processes change or scale up.
(Note: When implementing customizations in a regulated setting, always follow a proper development and validation methodology. The presence of these tools in NetSuite means everything is possible, but good governance is needed to ensure compliance is maintained.)
Case Studies and Real-World Examples
To put the above in context, here are a few examples of pharmaceutical and biotech organizations that leveraged NetSuite ERP to improve their operations and compliance:
-
Selecta Biosciences (USA) – Clinical-stage Biopharma scaling up: Selecta is a Nasdaq-listed biotech developing immunotherapies. They replaced fragmented on-premise software with NetSuite to unify financial management, time tracking, and project management as they prepared for growth intuitionlabs.ai. By having a single system, they synchronized R&D project planning with cash flow – ensuring the finance team could track spend by research milestone in real time. The result was improved visibility into the company’s burn rate and resource allocation. The FP&A Director noted that implementing NetSuite reduced back-office burdens, freeing the team to focus more on drug development rather than spreadsheet wrangling intuitionlabs.ai intuitionlabs.ai. This shows NetSuite’s value in a growing lab where agility and financial oversight are key.
-
BioMonde (UK & Global) – Global Wound Care Biotech: BioMonde produces a unique biosurgery product and expanded into multiple countries. They chose NetSuite OneWorld to manage complex multi-national operations, including manufacturing and distribution across Europe and the U.S. intuitionlabs.ai. With NetSuite, BioMonde gained a 360° view of financial, customer, product, and order data across all subsidiaries in real time intuitionlabs.ai intuitionlabs.ai. This visibility allowed them to slice and dice information quickly (e.g., to see batch inventory by region or sales by product) and make informed decisions. Critically for a regulated product, NetSuite helped them maintain control over quality and compliance while scaling – all batch inventory, quality holds, and distribution records were centrally visible, aiding consistent GMP compliance across sites intuitionlabs.ai. BioMonde’s story illustrates how NetSuite supports expansion into new markets without losing oversight of product integrity.
-
PharmChem, Inc. (USA) – Drug Testing Kit Manufacturer: PharmChem, a company making medical test kits, used NetSuite to automate and integrate processes that were previously manual intuitionlabs.ai. They implemented NetSuite’s ERP and CRM together, which streamlined order processing, invoicing, and client management. By moving to NetSuite, PharmChem significantly sped up their order-to-cash cycle and gained real-time visibility into customer orders and inventory intuitionlabs.ai intuitionlabs.ai. This was vital as they scaled production to meet demand. Executives reported that NetSuite freed staff from tedious data entry, allowing them to focus on customer service and business growth intuitionlabs.ai. The VP/CFO discussed at a NetSuite conference how automation via NetSuite was pivotal as the company grew – bridging front-office (sales orders, customer info) with back-office (fulfillment, billing) in one system intuitionlabs.ai. It underscores how even for manufacturing of regulated devices/kits, NetSuite’s integrated platform improves efficiency and control.
-
Recovery Healthcare (USA) – Clinical Service Provider: While not a manufacturer, this example is relevant for scale. Recovery Healthcare provides drug testing and monitoring services. After adopting NetSuite, they experienced 500% growth in three years with NetSuite as the backbone intuitionlabs.ai. The ERP scaled with their explosive expansion, showing the robustness of the system. They benefited from NetSuite’s ability to handle high growth without a dip in performance or control, which would be analogous to a manufacturing startup quickly ramping to commercial volumes with NetSuite handling it.
These case studies demonstrate tangible benefits that pharma and biotech organizations have realized with NetSuite: faster financial closes, improved data visibility, automated compliance processes, and capacity to handle rapid growth intuitionlabs.ai intuitionlabs.ai. Companies of various sizes – from small R&D labs to mid-sized commercial manufacturers – have successfully used NetSuite to streamline operations while meeting compliance requirements intuitionlabs.ai. The fact that NetSuite is used in life sciences companies going through IPOs, global expansions, and FDA audits speaks to its capability as a pharma-friendly ERP solution. Each of these references also highlights that NetSuite is not just an accounting system but a holistic platform that connects departments (lab, manufacturing, quality, finance, sales) in ways that legacy systems often struggle to do.
Conclusion
Implementing NetSuite ERP in a pharmaceutical manufacturing lab can be a transformative step towards operational excellence and compliance assurance. By leveraging core modules for finance, inventory, orders, and production – and extending them with pharma-specific quality and compliance tools – labs can manage all their critical functions in one integrated system. NetSuite’s support for FDA regulations (like 21 CFR Part 11 and cGMP requirements) through audit trails, electronic signatures, and validation documentation provides a solid foundation for meeting U.S. regulatory standards. Moreover, the platform’s scalability means it can accompany a company from startup in a single lab to commercialization across multiple facilities, all while maintaining control and visibility. Automation features such as workflows ensure that standard operating procedures are followed and documented, reducing the risk of human error. And through strategic integrations (with LIMS, MES, and validation software), NetSuite becomes the backbone of a wider digital ecosystem that ties together laboratory data, manufacturing execution, and compliance oversight. The end result for pharma professionals is a single source of truth for all manufacturing and quality data, real-time insights into operations, and confidence during audits that all necessary information is at their fingertips. In an industry where patient safety and product quality are non-negotiable, NetSuite offers the tools to run a lean, efficient, and compliant lab – whether you are producing small clinical batches or scaling up to supply the market. With careful implementation and validation, NetSuite ERP can help pharmaceutical manufacturers focus on what they do best (innovating and producing life-saving products) while the system handles the heavy lifting of process coordination, data integrity, and regulatory compliance.
DISCLAIMER
The information contained in this document is provided for educational and informational purposes only. We make no representations or warranties of any kind, express or implied, about the completeness, accuracy, reliability, suitability, or availability of the information contained herein. Any reliance you place on such information is strictly at your own risk. In no event will IntuitionLabs.ai or its representatives be liable for any loss or damage including without limitation, indirect or consequential loss or damage, or any loss or damage whatsoever arising from the use of information presented in this document. This document may contain content generated with the assistance of artificial intelligence technologies. AI-generated content may contain errors, omissions, or inaccuracies. Readers are advised to independently verify any critical information before acting upon it. All product names, logos, brands, trademarks, and registered trademarks mentioned in this document are the property of their respective owners. All company, product, and service names used in this document are for identification purposes only. Use of these names, logos, trademarks, and brands does not imply endorsement by the respective trademark holders. IntuitionLabs.ai is an AI software development company specializing in helping life-science companies implement and leverage artificial intelligence solutions. Founded in 2023 by Adrien Laurent and based in San Jose, California. This document does not constitute professional or legal advice. For specific guidance related to your business needs, please consult with appropriate qualified professionals.